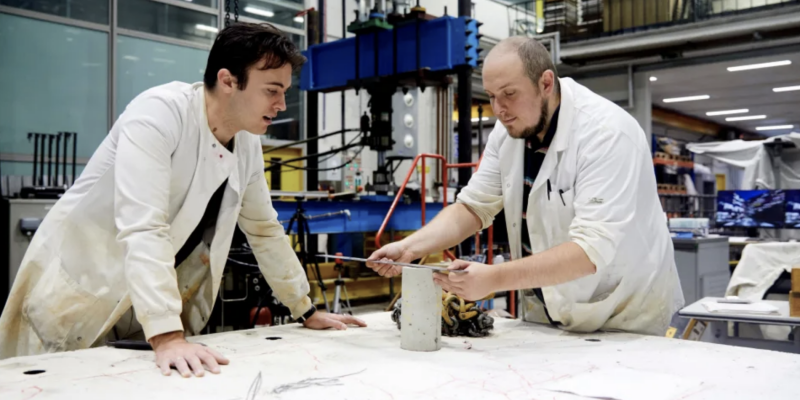
(CNN) – Nuestro mundo está construido de hormigón. Duradero y económico, es el material de construcción elegido para edificios, puentes y túneles. Pero su ubicuidad significa que tiene un gran impacto ambiental.
El concreto está hecho de agua mezclada con agregados como arena y grava, unidos por cemento, y es el cemento el que más contribuye a su huella de carbono.
El cemento Portland es el tipo más común y se produce cociendo cal en un horno. Se produjeron más de 4 mil millones de toneladas de cemento en 2021, lo que contribuyó con el 8% de las emisiones globales de CO₂, según el grupo de expertos Chatham House. Con la presión sobre la industria de la construcción para descarbonizar, los investigadores de todo el mundo están buscando formas de hacer que el concreto sea más ecológico.
“El concreto es un material tan fantástico y confiable que realmente vamos a tener dificultades para cortarlo en todas partes”, dijo Sam Draper, estudiante de doctorado en el Imperial College London. “Podemos hacer la transición a edificios de madera cuando sea posible, pero gran parte de nuestra infraestructura necesita concreto, y para hacer concreto necesitamos algún tipo de cemento”.
Draper y su colega investigador Barney Shanks han ideado una forma de hacer un cemento que, según dicen, puede producir hormigón sin emisiones de carbono.
Su proceso comienza con un mineral común llamado olivino, que dividen en magnesio y sílice. La sílice se usa para reemplazar directamente del 35 al 40 % del cemento Portland que se usa en el concreto, mientras que el magnesio se combina con dióxido de carbono (CO₂) para producir carbonato de magnesio, que luego se puede usar para materiales de construcción, incluidas alternativas a los ladrillos cocidos con arcilla y placas de yeso laminado.
Debido a que el CO₂ utilizado en el proceso puede capturarse de los conductos de desechos de las fábricas de cemento, que de otro modo habrían ido a la atmósfera, el concreto fabricado de esta manera es neutro en carbono, dice Draper, y el carbonato de magnesio es un almacén de carbono estable.
“Una de las cosas realmente buenas de la industria de la construcción desde la perspectiva del secuestro de carbono es que es grande y voluminosa, por lo que puede almacenar una gran cantidad de CO₂ allí”, dijo Draper.
“Y las cosas tienden a ser bastante permanentes, por lo que puede obtener un secuestro bueno y duradero. Usar CO₂ residual para hacer combustibles o algo está bien, y es circular, pero tan pronto como quemas ese combustible, el CO₂ desaparece. El entorno construido te brinda la oportunidad de bloquearlo realmente durante mucho tiempo”.
Después de comenzar sus pruebas en 2020, Draper y Shanks lanzaron una empresa llamada Seratech en 2021. Ahora, están a solo unas semanas de separar formalmente la empresa del Imperial College y poder recaudar fondos privados para una instalación piloto más grande capaz de producir unas pocas toneladas de cemento a la semana.
“Tiene que ser idéntico”
Draper dice que el cemento de Seratech funciona tan bien como el cemento Portland “estándar de oro”, y agrega que esto es vital para su aceptación en la industria de la construcción. “Para mí, este es un gran impulsor para estas tecnologías bajas en carbono”, dijo. “Tiene que verse igual, tiene que sentirse igual… tiene que ser idéntico, o la gente simplemente no lo usará en el mundo real. Y estoy muy feliz de decir que creo que lo hemos logrado bastante bien”.
El año pasado, la empresa ganó el Premio Obel, un premio internacional que “promueve la arquitectura al servicio de las personas y del planeta”. Al describir a los ganadores, el Premio Obel dijo: “Dada la enorme huella de carbono de la industria de la construcción, el proceso de Seratech tiene el potencial de reducir significativamente las emisiones incorporadas a nivel mundial y apoyar la construcción futura con bajas emisiones de carbono”.
Draper reconoce que el cemento es muy costoso en su etapa de investigación actual, pero dice que cuando se amplíe, los costos serán comparables con el cemento Portland. Agrega que Seratech planea comenzar a probar el cemento en edificios reales a principios de 2025 y espera tener un piloto industrial a gran escala para 2027, capaz de abastecer múltiples proyectos.
Otras nuevas empresas están encontrando formas de almacenar CO₂ directamente en el concreto. CarbonCure inyecta CO₂ capturado en el hormigón a medida que se mezcla, donde reacciona con el cemento para aumentar la resistencia del hormigón. Además de secuestrar CO₂, la compañía dice que esta fuerza adicional significa que el concreto se puede hacer con menos cemento. La compañía canadiense Carbicrete dice que puede reemplazar el cemento por completo, al combinar la escoria de desecho de la producción de acero con el carbono capturado de las plantas industriales.
Del agua salada al cemento
En los Emiratos Árabes Unidos (EAU), los investigadores están trabajando en un proceso para reducir la huella de carbono del hormigón mientras abordan otro problema ambiental.
Los Emiratos Árabes Unidos dependen de la desalinización del agua de mar para la mayor parte de su agua potable, pero el proceso produce agua salada, llamada salmuera, como subproducto, que se bombea de nuevo al océano, aumentando su salinidad, lo que puede dañar la vida marina.
Kemal Celik, profesor asistente de Ingeniería Civil y Urbana en NYU Abu Dhabi, descubrió que la salmuera contiene minerales útiles, incluidas altas concentraciones de magnesio.
“Lo que estamos haciendo es usar esta salmuera rechazada de la planta desalinizadora y aplicar una química muy simple”, dijo. Su equipo ha desarrollado un proceso para separar los componentes sólidos y líquidos de la salmuera y luego usar el componente de magnesio para hacer cemento.
“El cemento a base de magnesio no es un nuevo tipo de cemento… pero la fuente de carbonatos de magnesio generalmente proviene de la industria minera”, explica Celik. Producir cemento convencional a base de magnesio requiere calentamiento y emite CO₂, dice, y agrega que crearlo a partir de salmuera residual es rentable y respetuoso con el medio ambiente.
Celik dice que su investigación se encuentra actualmente en la etapa de prueba de concepto, trabajando con 4000 a 5000 litros de salmuera por día, pero está buscando producir el material a una escala lo suficientemente grande como para trabajar con la industria de la construcción.
“Creo que el mayor desafío para nosotros es la industria misma”, explicó. “La industria de la construcción es una de las industrias más antiguas y es posible que tengamos cierta resistencia a cambiar el material que (está) utilizando actualmente. En ese sentido, necesitamos aumentar la conciencia en la industria y el público”.
Pero Celik está decidido a estar a la altura del desafío. “Como investigador, tenemos que servir a la comunidad. Es por eso que estoy tan motivado con nuestra investigación que podría ayudar un poco al mundo en términos de combatir el cambio climático”.
Deja tu comentario